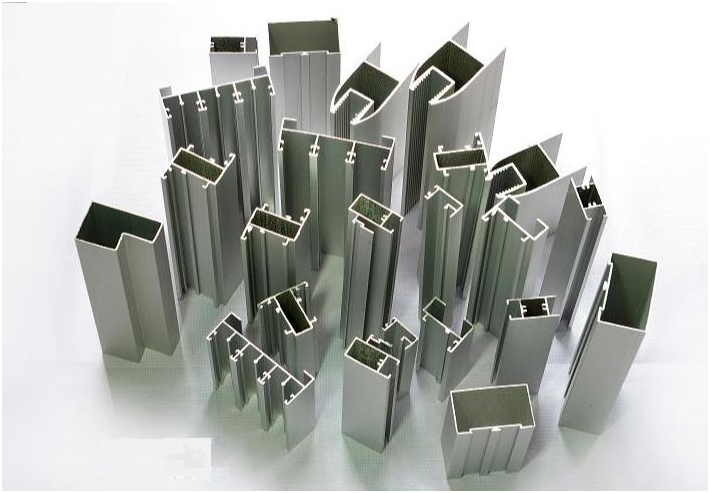
Aluminum Extrusions
- 30 years of factory manufacturing experience
- More than 5000 kinds of molds for you to choose
- ISO 9001-2008 Authorization
- Annual sales of 200 million US dollars
Your High Quality Aluminum Profile Manufacturer
ManufacturerExtruded Aluminum Profile
The annual production capacity is 100,000 tons sales team responded quickly
Extruded Aluminum Profile Manufacturer in China Certified
A professional manufacturer of extruded aluminum profiles in China,Possess ISO 900 quality management system certification, a high-tech enterprise certificate granted by the state and multiple patent certificates
Professional business team
With advanced internal quality testing facilities, more than 50 QC testing professionals; before delivery, product inspection and product video or pictures will be sent to you to ensure product quality and relieve your worries.
Fast delivery
has a stable delivery time. The finished products can be shipped within 7 days, and the delivery time of extruded products is 14 days. We have 25 extrusion machines and can ship quickly
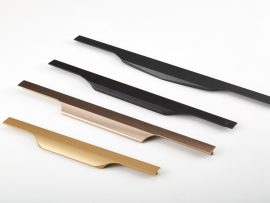
Aluminum Cabinet Handle
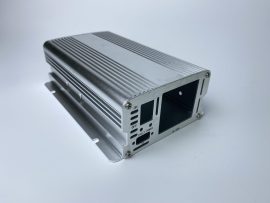
Aluminum Motor Housing
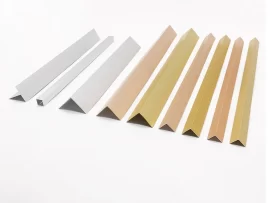
Aluminum Angle
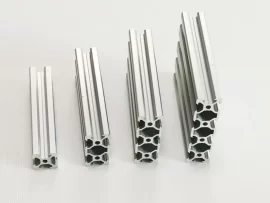
Assembly Line Profiles
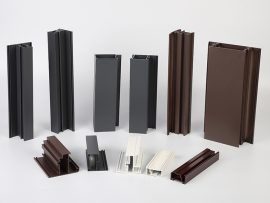
Window & Door Profiles
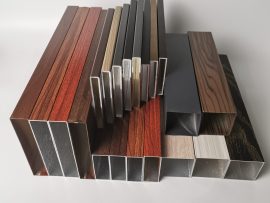
Aluminum Tube
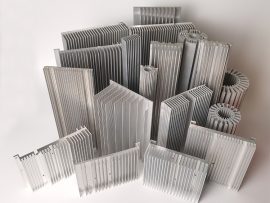
Heat Sink
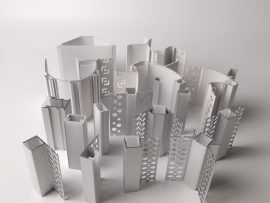
LED Profiles
Your professional extruded aluminum profile manufacturer
GUANGDONG DREAM STAR SUPPLY CHAIN CO.,LTD extruded aluminum profiles are products made through the aluminum extrusion process, mainly including industrial aluminum profiles and architectural aluminum profiles. Extrusion is to put the aluminum profile into the mold and then extrude it through the extrusion machine. The conventional profile has a mold, but the special profile needs to be opened again. Can provide the aluminum products you want, with more than 30 years of experience in aluminum production, is a manufacturer worthy of your trust
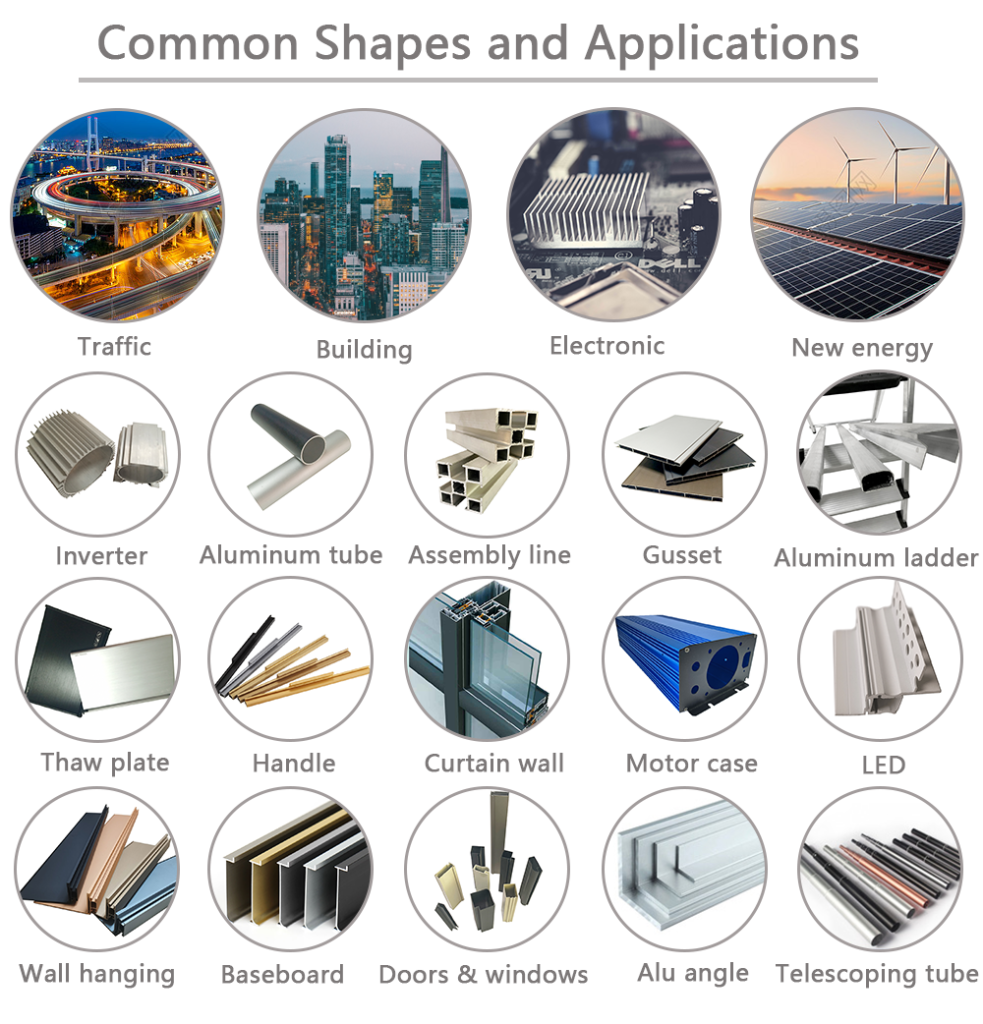
GUANGDONG DREAM STAR SUPPLY CHAIN CO.,LTD Aluminum Profile Extrusion: Extrusion is the means of profile forming. First, design and manufacture the extrusion die according to the cross-section of the profile product. The aluminum rod is first heated to a certain temperature to reach the critical point of aluminum liquefaction, and then cut, hot-sheared, and sent to the extrusion machine. Rods are extruded from a die. Extrude the desired cross-sectional shape through the extrusion die
WE can provide the following surface treatments: sandblasting, polishing, brushing, electroplating, spraying. With Germany’s advanced anodizing production line, it can meet your requirements for high-quality extruded aluminum profiles
Let’s Support Your Bussiness and Reduce Cost For You
GUANGDONG DREAM STAR SUPPLY CHAIN CO.,LTD can custom your Aluminum Extrusions , Also can design your own Products, Even If idea ONLY.
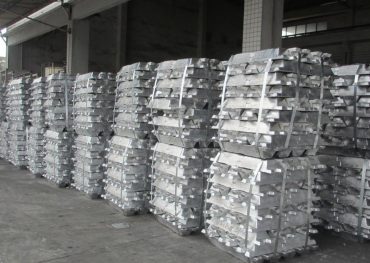
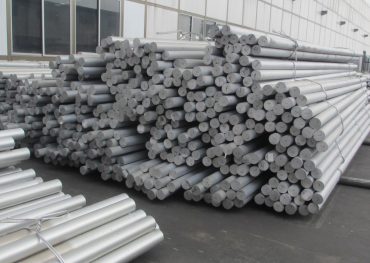
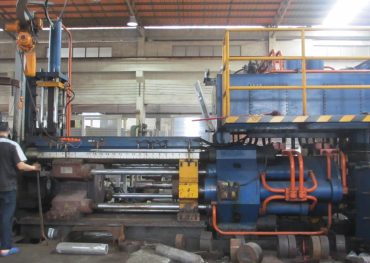

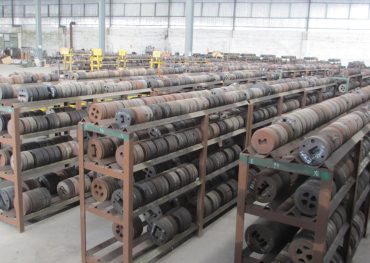
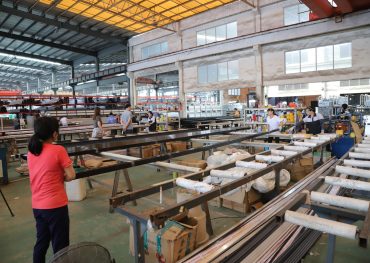
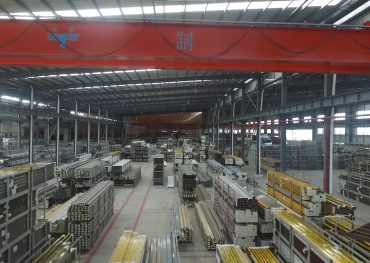
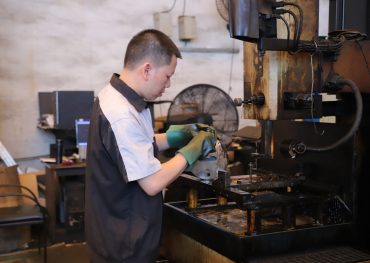
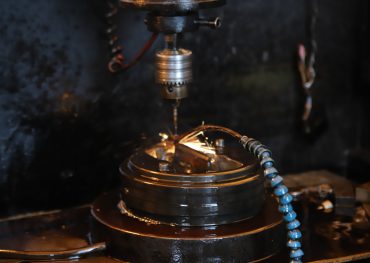
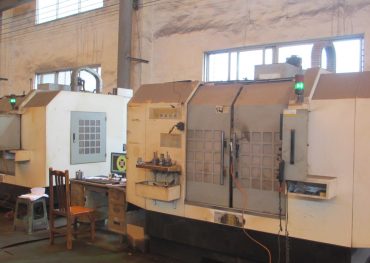
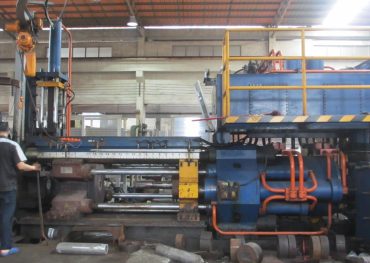
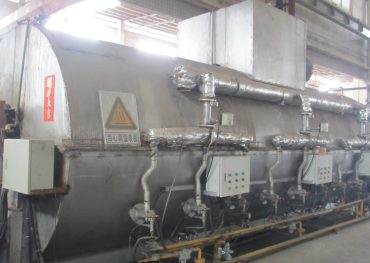
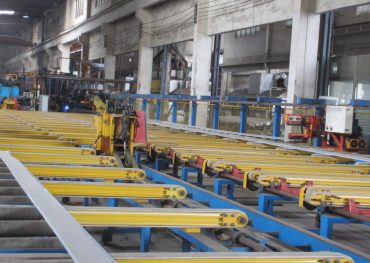
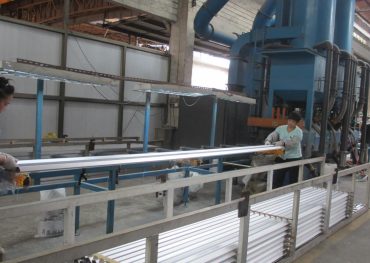
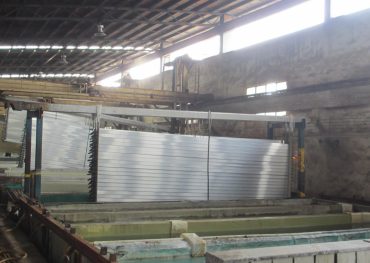
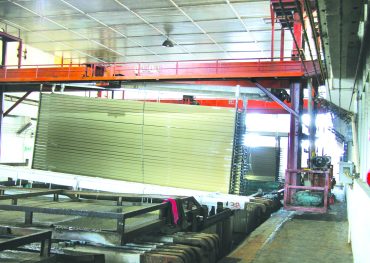
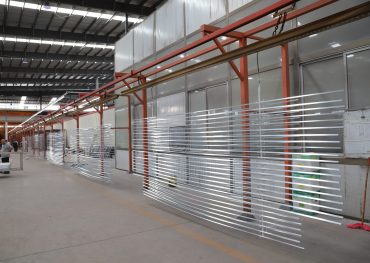
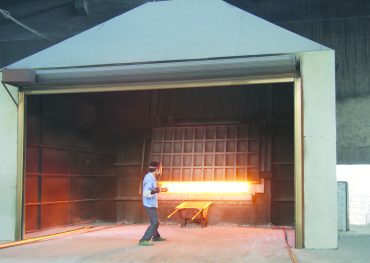
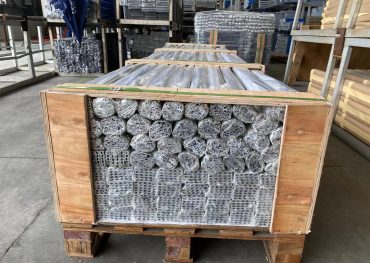
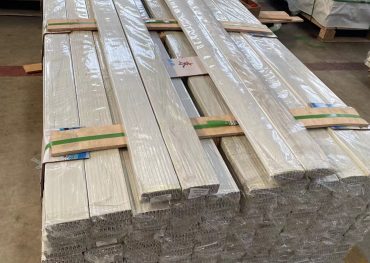
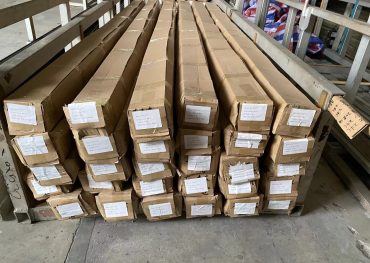
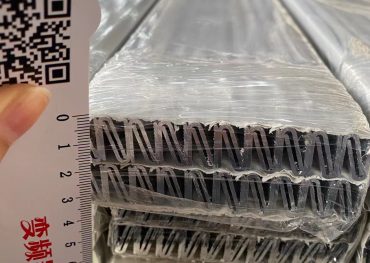
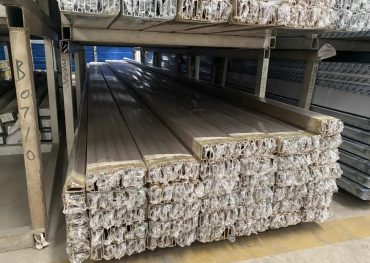
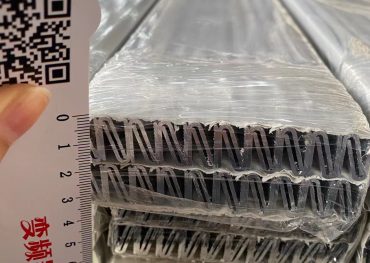
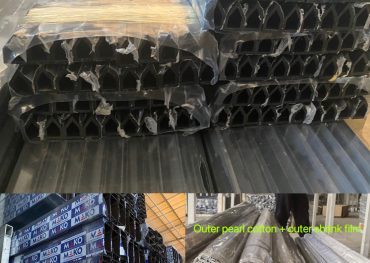
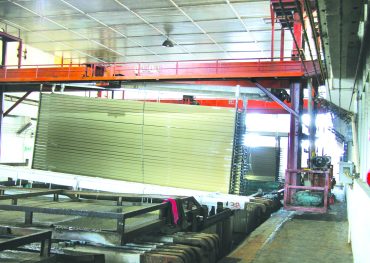
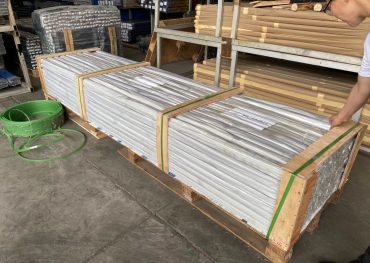
Your best quality extruded aluminum profile manufacturer
GUANGDONG DREAM STAR SUPPLY CHAIN CO.,LTD extruded aluminum profiles are widely used, involving transportation industry (engine block, transmission housing, panel), construction industry (windows, doors, atrium and skylight), electronics industry (motor housing, high heat dissipation radiator), lighting industry , solar industry, etc.
Advantages of extruded aluminum profiles: 1. Small density and light weight; 2. Easy surface treatment and strong corrosion resistance after treatment; 3. Good plasticity, processing, and casting properties; 4. Aluminum profiles have good thermal conductivity and electrical conductivity. It has good ductility; 5. It can be used to make light alloys with many metal elements, and the material is excellent.
We provides one-stop service from aluminum extrusion production to aluminum deep processing. Deep processing services include cutting, drilling, tapping, milling, bending, straightening, etc. The cost is cheaper than CNC factories, helping you develop and design differentiated products , gain more market share
We has a full set of production lines from aluminum ingot casting, mold manufacturing, extrusion, anodizing, coloring, electrophoretic coating, electrostatic powder coating, wood grain production line, strip heat insulation, etc.
We has a professional R&D team with more than 20 years experience in oem and odm, and exported to more than 50 countries. One-stop aluminum profile manufacturer, new technology for finishing, we position ourselves as a global aluminum profile solution provider based in China
Aluminum Extrusion: The Ultimate Guide
The aluminum extrusion process is to put the aluminum ingot into the extrusion cylinder, apply pressure to the aluminum through the extrusion shaft, and make it extrude from the die hole with a given shape and size, and produce plastic deformation to obtain the required extrusion. A processing method for pressed products.
- Aluminum profile extrusion process and working principle?
- Extrusion Model Classification
- aluminum extrusion die
- Detailed process of extruded aluminum profiles
- Factors to be considered in the design of extruded aluminum profiles
- The wall thickness of aluminum profiles that we can provide
- Alloy State Differences – Aging
- Performance-enhancing surface treatments for aluminum extrusions
- aluminum extrusion quality assurance
- Advantages of powder coating
- Packaging method of aluminum profile
- Application of aluminum profiles
Aluminum profile extrusion process and working principle?
Aluminum profile extrusion is a plastic processing method that applies external force to the aluminum ingot contained in the extrusion cylinder to make it flow out of a specific die hole, so as to obtain the required cross-sectional shape and size. The figure below shows the aluminum profile extrusion Schematic diagram of press forming;
Aluminum profiles can be extruded according to the different states of the metal in
the barrel, according to the stress and strain state of the metal in the extrusion
barrel, the metal flow direction, the lubrication state, the extrusion temperature,
the extrusion speed, the structural form of the equipment, and the type of tools Or
the structure and shape According to the shape or quantity of the blank, the shape
or quantity of the aluminum profile, etc., the extrusion forming method can be
divided into the following methods;
Extrusion Model Classification
According to extrusion direction | Forward Extrusion (Forward Extrusion) |
reverse extrusion (back extrusion) | |
lateral extrusion | |
According to deformation characteristics | Planar Deformation Extrusion |
Axisymmetric Deformation Extrusion | |
—Share three-dimensional deformation extrusion | |
According to lubrication state | Non-lubricated extrusion (adhesive friction extrusion) |
Lubricated extrusion (conventional lubricated extrusion) | |
glass lubricated extrusion | |
Ideally lubricated extrusion (hydrostatic extrusion) | |
Divided by extrusion temperature | cold extrusion |
warm extrusion | |
hot extrusion | |
Divided by extrusion speed | Low speed extrusion (common extrusion) |
high speed extrusion | |
Impact extrusion (ultra-high speed extrusion) |
Divided by mold type or mold structure | flat die extrusion |
Cone extrusion | |
split die extrusion | |
Extrusion with perforated needle (also can be divided into fixed needle extrusion and follower needle extrusion) | |
According to the shape or number of blanks | Round billet extrusion (round extrusion barrel extrusion) |
Flat billet extrusion (flat extrusion simply extruded) | |
multiple billet extrusion | |
Composite Billet Extrusion | |
According to the shape or number of aluminum profiles | Toon extrusion |
Tube Extrusion | |
Solid Aluminum Extrusion | |
Hollow Aluminum Extrusion | |
variable section extrusion | |
Single product extrusion (single hole die extrusion) | |
Multi-product extrusion (porous die extrusion) | |
by device type | vertical extrusion |
horizontal extrusion | |
conform continuous extrusion |
aluminum extrusion die
For product structure design engineers, although we do not design aluminum extrusion dies, understanding the most basic extrusion die structure and the mechanism of how to shape different extrusion shapes will help in extrusion. During the design of the extrusion, the optimized design can reduce the cost of the mold and improve the production efficiency of the extrusion.
2.1 What is an extrusion die?
Extrusion dies are basically thick circular steel disks containing one or more openings to form the desired profile. They are usually made of H-13 die steel and are heat treated to withstand the pressure and heat of hot aluminum passing through the die.
Although aluminum appears to be a very soft metal,it takes a lot of pressure to push a solid aluminum ingot (billet) through a thin,porous aluminum extrusion die to form the desired shape.
2.2 The difference between solid mold, hollow mold and semi-hollow mold
Molds for solid aluminum profiles
It can be extruded by an extruder just by processing a forming hole on the mold. Such as, for example, solid bars, angle aluminum and channel aluminum.
hollow mold
Hollow molds produce shapes with one or more voids, for example, simple round tubes, rectangular tubes, or complex multi-void t-slots.
To extrude hollow shapes, a split die is usually used. It is made of two interlocking pieces – the mandrel and the cap. The mandrel forms the internal feature of the profile and has a number of apertures separated by webs or legs for support. The cap forms the exterior feature of the profile and is assembled with the mandrel. During the extrusion process, the hot billet of aluminum will enter through the mandrel and exit through the cap.
3. Semi-hollow mold
Like hollow shapes, semi-hollow shapes have one or more voids. The difference, though, is that the voids are not completely closed, there are gaps or openings between them.
It’s a bit of a mix between the previous two types. As it turns out, there is often only a small difference between a solid shape and a semi-hollow shape.
For example, a wide aluminum trough with a partially closed void is considered solid. On the other hand, very narrow aluminum slots may be considered semi-hollow.
2.3 Life of extrusion die
Heat buildup and uneven pressure caused by the design of aluminum extrusions (such as thin walls, uneven wall thickness, and protruding features) are the biggest killers of extrusion die life.
An experienced extrusion die engineer can design the die to control heat and uneven pressure, and reduce the extrusion speed to prolong the life of the die, but eventually the die must be replaced.
Before designing aluminum extrusions, product structural design engineers should understand which design features will most significantly affect tooling costs. Where possible, changing the design of the aluminum extrusion section, setting appropriate tolerances, and selecting the appropriate aluminum alloy material can save the processing cost of the aluminum extrusion die.
2.4. The mold processing cycle is short and the cost is low
The aluminum extrusion mold is simple, the processing cycle is short, and the cost is low. This is AEC’s comparison of aluminum extrusion and other processes, for reference only.
Process | Typical Tooling Cost | Typical Tooling Lead Time |
Vinyl Extrusion | $1,500 and up | 4 weeks or less |
lnjection Molding | $25,000 and up | 20 weeks or less |
Die Casting | $25,000 and up | 20 weeks or less |
Roll Forming | $30,000 and up | 13 weeks or less |
Stamping | $5,000 and up | 7 weeks or less |
Aluminum Extrusions | $500 to $5,000 | 2 weeks or less |
Detailed process of extruded aluminum profiles
Extruded aluminum profile is a common processing method, and its process is mainly divided into raw material preparation, aluminum profile extrusion, aluminum profile cooling and processing. The following is the detailed process of aluminum profile extrusion:
1. Raw material preparation
Aluminum alloy materials are usually used in the production of aluminum profiles. It is necessary to heat the aluminum alloy billet to a certain temperature to reach a softened state. Generally, the extrusion temperature of aluminum alloy is between 320 and 520 °C. At this time, the aluminum alloy billet can be processed through an extrusion die.
2. Aluminum profile extrusion
During the extrusion process, the aluminum alloy billet is placed in a special heating furnace for the extrusion machine, thereby heating and softening the aluminum alloy billet. When the proper temperature is reached, the aluminum alloy billet is pressed into the extrusion die by the rotating cylinder. In the mold, the aluminum alloy material is extruded under high pressure to form an aluminum profile.
3. Aluminum profile cooling
The extruded aluminum profile needs to be cooled in order to allow the aluminum profile to return to its normal solid state. During this process, the aluminum profile is continuously sprayed with water to prevent secondary deformation.
4. Processing
Aluminum profiles need to be processed after cooling in order to meet different industrial needs. Common processing methods include cutting, welding, drilling, etc.
Factors to be considered in the design of extruded aluminum profilessize shape Aluminum Alloy Selection tolerance Extrusion Ratio, Tongue Ratio and Surface Finish Finally, assembly issues also need to be considered. Aluminum profiles are often assembled with other parts in practical applications, so it is necessary to consider the degree of fit and connection with other parts to ensure the smoothness and correctness of the product assembly process. In general, the design of extruded aluminum profiles requires comprehensive, systematic and scientific consideration of various factors to ensure that the quality and performance of the product meet the application requirements. Only in this way can we create better aluminum profile products and bring more convenience and benefits to people’s life and work. |
The wall thickness of aluminum profiles that we can provideIn extruded aluminum profiles, wall thickness is an important factor in determining its strength and durability. In extruded aluminum profiles, the wall thickness that we can provide is divided into three categories, which are light, medium and heavy. These different wall thicknesses are selected based on your specific application needs. The wall thickness of light extruded aluminum profiles is generally between 1.0mm and 2.0mm. This type of aluminum profile is very suitable for the fields of architectural doors and windows, furniture, aircraft models and electronic products. The wall thickness of medium-sized extruded aluminum profiles is generally between 2.0mm and 3.0mm. This type of aluminum profile is widely used in larger building structures and mechanical equipment. The wall thickness of heavy-duty extruded aluminum profiles is generally above 3.0 mm. This type of aluminum profile is commonly used in the manufacture of industrial and architectural structures for support or load bearing. In short, extruded aluminum profiles have a variety of wall thicknesses for you to choose from. Selecting the appropriate wall thickness according to your specific application requirements can ensure that your products have better performance, strength and durability, and make them more durable Play a more important role in a wide range of application fields. |
Alloy State Differences – AgingAlloys are materials made by mixing two or more metal or nonmetal elements. It is precisely because alloys have more excellent physical and chemical properties than single-element materials, making them widely used in industrial production, construction, energy, aerospace, automobile manufacturing and other fields. However, in the use of alloys, one needs to be aware of a state difference called aging. Aging refers to the phenomenon that the properties of an alloy will gradually change over time after receiving a specific heat treatment. The strength and hardness of the alloy after aging heat treatment will gradually increase due to the continuous increase of precipitated phases. At the same time, aging will also have a certain impact on the ductility and toughness of the alloy. Since the crystallization state of the alloy and the number and size of precipitated phases change over time, when using the alloy, the aging state needs to be considered according to the specific application scenario and requirements. However, the aging state is not a defect of the alloy. On the contrary, for different application environments and uses, the aging state can provide more excellent performance and more adequate utilization. For example, the axles of air vehicles and the blades of aircraft engines need to have characteristics such as high strength, high hardness and high temperature stability. These properties happen to be achieved through aging states. In short, the aging state is one of the unique state characteristics of alloy materials. In a specific application environment, by choosing an appropriate aging state, alloy materials can produce excellent performance with better performance, so as to better serve our production and life. . |
Performance-enhancing surface treatments for aluminum extrusionsIn order to improve the performance of aluminum extrusion products, surface treatment is a very important step. Several surface treatment methods to optimize the surface of aluminum extrusion are introduced below. 1. Oxidation treatment Oxidation treatment is a common surface treatment method, which can improve the corrosion resistance, wear resistance and decoration of aluminum by forming an oxide layer on the surface of aluminum extrusion. Oxidation treatment methods include sulfuric acid oxidation, sulfuric acid chromic acid oxidation and nitric acid oxidation. Advantages of oxidation treatment: 2. Electroless chrome plating Electroless chrome plating is performed using a chemical reaction instead of electroplating. It is a method of forming a thin, dense layer of chromium on the surface of aluminum, which improves the corrosion resistance and decorative properties of aluminum. Advantages of Electroless Chrome Plating 3. Anodizing Anodizing is an electrochemical surface treatment method that can improve the corrosion resistance, wear resistance and electrical properties of aluminum by forming a dense and uniform oxide layer on the surface of aluminum. In addition, anodizing can also be used for dyeing and decoration. dvantages 4. Powder Coating It is a coating technology that sprays and heats the powder on the surface of aluminum products to adhere and form a coating, thereby providing a layer of protection and enhancing the aesthetics and durability of the material. Compared with sandblasting, powder spraying is more uniform and stable |
aluminum extrusion quality assurancewe is committed to providing high-quality extrusion products. Therefore, we ensure that every production stage of the extrusion process is supported by state-of-the-art quality control methods. we can provide you with the best solution and the most advanced equipment. we conducts continuous employee training to minimize errors and technical defects. Every stage of the extrusion process is carried out according to the latest quality certifications such as ISO 9001. we is proud of its strict on-line monitoring of the aluminum extrusion process and careful inspection of the extrusion products. |
Advantages of powder coating Guarantee the quality of raw materials Quality of machinery and equipment Standardization of process flow Personnel quality and quality awareness |
Packaging method of aluminum profile一.Non-woven fabric + kraft paper packaging1. Wrap non-woven fabrics: Lay the aluminum profiles neatly according to the direction, separate them with non-woven fabrics in the middle, wrap the non-woven fabrics completely to tie the aluminum profiles, and then tie them tightly with tape. 2. Wrapping with kraft paper: Move the aluminum profile wrapped with non-woven fabric to the packaging machine, wrap it evenly with kraft paper, and wrap both ends tightly with tape. 3. Paste the certificate of conformity: a certificate of conformity shall be pasted on the outside of each package of aluminum profiles, indicating the manufacturer of the product, the name of the manifest, length, quantity, and the name of the consignee. Generally, aluminum profiles with surface oxidation treatment must be wrapped with non-woven fabric first, and then with kraft paper. For the base material, there is no need to wrap non-woven fabrics, and kraft paper is wrapped at right angles. Surface requirements 二. Packaging:1. Metal lifting frame: In order to facilitate the lifting and unloading of goods, a metal lifting frame can be built. 2. Pallet packaging: suitable for sawn and processed aluminum profiles, generally within two meters in length, like a solar frame, the long and short sides are stacked on the pallet, and wrapped with stretch film. If it is exported, it needs to be fixed with wooden boards around it, covered with cartons outside, and then packed with packing ropes. 3.Wooden box packaging: This service is mostly used by customers who need to send bulk goods. In order to prevent the aluminum profile from being crushed by other heavy cargo during transportation, it is recommended that customers who need to send bulk cargo use wooden boxes. Among them, some are packed in wooden boxes and need to be fumigated. |
Application of aluminum profilesAluminum profile is a widely used material, mainly composed of aluminum alloy and other elements. It has excellent corrosion resistance, strength and lightweight characteristics, so it is widely used in various industries. Construction sector door frame wall decoration ceiling heat sink Transportation field car 1. Body structure: As one of the body structure materials, aluminum profiles can effectively reduce the weight of the vehicle. The application of aluminum profiles can make the body more energy-saving and environmentally friendly, improve the fuel efficiency of the car and reduce exhaust emissions train In terms of appearance, the body of the train is made of a large number of aluminum materials, making it lightweight and high-strength. In addition, aluminum profiles are also widely used in the construction of internal facilities of trains, such as frames, doors, windows and other components, as well as assembly between carriages to form train connections. The aluminum profile carriage is more convenient and faster in assembly and disassembly, and has a wider scope of application. It has higher load-bearing capacity and stability, which effectively improves the safety of the train. airplane In aviation manufacturing, in addition to considering the strength requirements of the material, its weight also needs to be considered. In life, the application of aluminum profiles is also very extensive. For example, in the kitchen, it can be used to make various kitchen utensils, such as kitchen wardrobes, ovens, and microwave ovens. Their light weight and high strength make our lives more convenient. |